Obrnite se na nas
Telefon
Slovenija
19.09.2019
Johann Borgers GmbH uses the technology platform MultiMaterial-Welding by KVT-Fastening
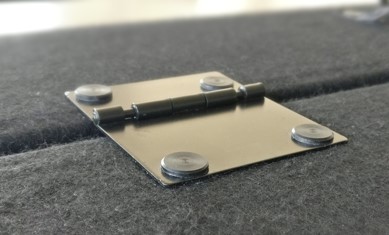
Johann Borgers GmbH develops custom damping, insulation and equipment solutions for a number of different passenger car and truck models. Different joining techniques are used depending on the installation location on the outer body as well as in the engine, passenger and trunk compartments. With the new MultiMaterial -Welding (MM-W) technology from KVT-Fastening, Borgers was able to implement a fastening variant for a trunk floor with a paper honeycomb core for a luxury SUV, which could not be realized from a technical point of view using conventional methods.
Products beyond the (DIN) standard
Looking at and reaching into the shelf with DIN parts and other standard joining elements is routine for Dipl. Ing. Mark Maibom, who is responsible for joining technology in the Industrial Engineering division at Johann Borgers GmbH: “The standardization of joining techniques of welding, adhering, riveting and bolting has a high priority across all locations at Borgers. Because this is the only way we can ensure a consistent process reliability in the production and assembly of our products. In the division of Industrial Engineering for the automotive sector, we nevertheless see ourselves as faced with new challenges.” One reason for this is the high variance of the product portfolio: Among other things, Borgers produces acoustically effective trim and damping parts for side panels, trunk floors and rear shelves in the interior. In addition, complex assembly units are produced, such as several square meter large truck roof linings with built-in handles, lights and storage compartments as well as passenger car rear shelves with built-in speakers and sun blinds or driver seat trim with lighting elements. There are also exterior underbody protection panels and wheel arch liners.
All fastening points under control
A variety of different materials is processed to be able to meet individual customer requirements. These range form thermoplastic and duroplastic supports to needle non-woven material, polyurethane films and genuine leather applications as decor. Maibom adds: “This results in a variety of different fastening points in or on the vehicle that are located either directly on the vehicle body or on various metal or plastic supports. The respective connection is welded, adhered, riveted or bolted depending on the material and the customer requirements. A large portion of these connections can be made reliably and economically by using DIN parts and other fastening elements. However, some requirements cannot be met at all from these viewpoints or not to the standard that the customer and we place on our products from a technical point of view as well as with respect to sustainability.”
New technology wanted and ...
This is why the development team, of which Mark Maibom is an integral part, is always looking for new possibilities to introduce reinforcements or fastening points into attachments even more efficiently: “The aim is always to achieve simplification in as many areas as possible: with the number of individual product parts, with the weight, assembly effort and ultimately the subsequent recycling.” At Borgers, that is why so-called “FIP” parts (Functional Integrated Parts) are increasingly being used, such as the handles with built-in latching, which do not require any additional screws.
... MultiMaterial Welding found
Maibom found out about an event on the topic of “WoodWelding” through a colleague. In this process used in the furniture industry, ultrasound is used to weld plastic parts into wood materials. This same technology is used in the medical sector under the name “BoneWelding” to accelerate the healing of broken bones. The team did some brief research and found out about the MultiMaterial -Welding (MM-W) version designed for industrial use. In this process, thermoplastic fasteners are “pushed” through the top layer of porous sandwiched materials using ultrasound within a second without any pre-drilling or pre-treatment required. The friction between the connector surface and the component ensures that the surface of the fastener itself becomes the joining material. Because of its material hardness, however, it retains its shape and can be loaded immediately after the joint has been released. Mark Maibom has this to say about it: “This technology seems like it was made for us. Because a lot of our products are based on exactly these porous PUR sandwich components for which the MM-W was developed. Up until now, we have been using the possible known joining techniques for these components. However this was always associated with extra work and limitations, such as bore hole pre-work and post-work and observing the hardening and drying times.”
The ideal project for the new technology
Dipl.-Ing. Gregor Eckhard, managing director of MultiMaterial-Welding GmbH, was contacted quickly. The Borgers development team and MM-W then carried out the first material tests. At the same time, the order lead time for suitable products for an initial pilot project was reviewed. Maibom said about it: “Before the first practical tests, however, we used a calculator: Because depending on the type of application and amount of calculated machine costs, this had both positive and negative effects. After reviewing several possible customer projects, it ultimately was determined that this was ideal for MM-W both from a technical and economical standpoint.”
The specific requirement is a lightweight and highly stable trunk floor with paper honeycomb core. Depending on the passenger car equipment ordered, this is needed by the customer in different decors as well as with or without other mounted details. In addition to a grip strap, each variant has a number of fastening elements that engage in the vehicle body and center the trunk floor over the vehicle body. The special challenge is that these fasteners must be placed extremely close to the edge of the trunk floor. This is why the use of drive-in nuts, rivets or the like is ruled out. This would either damage the edge area or the fastener would protrude visibly. Both are “unacceptable” according to Mark Maibom.
MultiMaterial-Welding meets all requirements
Special weld-in pins were developed together with KVT-Fastening because of the specific requirement. The first version had a metric thread. Then a lower cost solution with a self-tapping screw was developed. The MM-W technology makes it possible to place these fastening elements directly on the edge without being seen from above in order to meet customer requirements. In addition, the method was convincing with respect to the tensile forces and weight loads occurring while driving as soon as there are heavy loads in the trunk. Mark Maibom has this to say about it: “The final solution is the ideal standard form a technical and economic point of view. This is also true of the process reliability: Because every welding process is subject to continuous monitoring. Any material weakness in the trunk floor that impairs a secure hold will immediately be visible this way.”
Mark Maibom draws an initial conclusion: “With the MultiMaterial Welding technology, we have entered completely new territory, which of course was generally a risk. That’s all the more reason why we are happy that it all worked out smoothly – and not just from a technical point of view: The cooperation with the teams at MultiMaterial-Welding GmbH and KVT-Fastening GmbH was positive in every way. Otherwise the current project could not have been implemented in this way. Based on the experience so far, we are currently checking what other projects are suitable for this or which FIP parts can be developed or improved from this.”
Products beyond the (DIN) standard
Looking at and reaching into the shelf with DIN parts and other standard joining elements is routine for Dipl. Ing. Mark Maibom, who is responsible for joining technology in the Industrial Engineering division at Johann Borgers GmbH: “The standardization of joining techniques of welding, adhering, riveting and bolting has a high priority across all locations at Borgers. Because this is the only way we can ensure a consistent process reliability in the production and assembly of our products. In the division of Industrial Engineering for the automotive sector, we nevertheless see ourselves as faced with new challenges.” One reason for this is the high variance of the product portfolio: Among other things, Borgers produces acoustically effective trim and damping parts for side panels, trunk floors and rear shelves in the interior. In addition, complex assembly units are produced, such as several square meter large truck roof linings with built-in handles, lights and storage compartments as well as passenger car rear shelves with built-in speakers and sun blinds or driver seat trim with lighting elements. There are also exterior underbody protection panels and wheel arch liners.
All fastening points under control
A variety of different materials is processed to be able to meet individual customer requirements. These range form thermoplastic and duroplastic supports to needle non-woven material, polyurethane films and genuine leather applications as decor. Maibom adds: “This results in a variety of different fastening points in or on the vehicle that are located either directly on the vehicle body or on various metal or plastic supports. The respective connection is welded, adhered, riveted or bolted depending on the material and the customer requirements. A large portion of these connections can be made reliably and economically by using DIN parts and other fastening elements. However, some requirements cannot be met at all from these viewpoints or not to the standard that the customer and we place on our products from a technical point of view as well as with respect to sustainability.”
New technology wanted and ...
This is why the development team, of which Mark Maibom is an integral part, is always looking for new possibilities to introduce reinforcements or fastening points into attachments even more efficiently: “The aim is always to achieve simplification in as many areas as possible: with the number of individual product parts, with the weight, assembly effort and ultimately the subsequent recycling.” At Borgers, that is why so-called “FIP” parts (Functional Integrated Parts) are increasingly being used, such as the handles with built-in latching, which do not require any additional screws.
... MultiMaterial Welding found
Maibom found out about an event on the topic of “WoodWelding” through a colleague. In this process used in the furniture industry, ultrasound is used to weld plastic parts into wood materials. This same technology is used in the medical sector under the name “BoneWelding” to accelerate the healing of broken bones. The team did some brief research and found out about the MultiMaterial -Welding (MM-W) version designed for industrial use. In this process, thermoplastic fasteners are “pushed” through the top layer of porous sandwiched materials using ultrasound within a second without any pre-drilling or pre-treatment required. The friction between the connector surface and the component ensures that the surface of the fastener itself becomes the joining material. Because of its material hardness, however, it retains its shape and can be loaded immediately after the joint has been released. Mark Maibom has this to say about it: “This technology seems like it was made for us. Because a lot of our products are based on exactly these porous PUR sandwich components for which the MM-W was developed. Up until now, we have been using the possible known joining techniques for these components. However this was always associated with extra work and limitations, such as bore hole pre-work and post-work and observing the hardening and drying times.”
The ideal project for the new technology
Dipl.-Ing. Gregor Eckhard, managing director of MultiMaterial-Welding GmbH, was contacted quickly. The Borgers development team and MM-W then carried out the first material tests. At the same time, the order lead time for suitable products for an initial pilot project was reviewed. Maibom said about it: “Before the first practical tests, however, we used a calculator: Because depending on the type of application and amount of calculated machine costs, this had both positive and negative effects. After reviewing several possible customer projects, it ultimately was determined that this was ideal for MM-W both from a technical and economical standpoint.”
The specific requirement is a lightweight and highly stable trunk floor with paper honeycomb core. Depending on the passenger car equipment ordered, this is needed by the customer in different decors as well as with or without other mounted details. In addition to a grip strap, each variant has a number of fastening elements that engage in the vehicle body and center the trunk floor over the vehicle body. The special challenge is that these fasteners must be placed extremely close to the edge of the trunk floor. This is why the use of drive-in nuts, rivets or the like is ruled out. This would either damage the edge area or the fastener would protrude visibly. Both are “unacceptable” according to Mark Maibom.
MultiMaterial-Welding meets all requirements
Special weld-in pins were developed together with KVT-Fastening because of the specific requirement. The first version had a metric thread. Then a lower cost solution with a self-tapping screw was developed. The MM-W technology makes it possible to place these fastening elements directly on the edge without being seen from above in order to meet customer requirements. In addition, the method was convincing with respect to the tensile forces and weight loads occurring while driving as soon as there are heavy loads in the trunk. Mark Maibom has this to say about it: “The final solution is the ideal standard form a technical and economic point of view. This is also true of the process reliability: Because every welding process is subject to continuous monitoring. Any material weakness in the trunk floor that impairs a secure hold will immediately be visible this way.”
Mark Maibom draws an initial conclusion: “With the MultiMaterial Welding technology, we have entered completely new territory, which of course was generally a risk. That’s all the more reason why we are happy that it all worked out smoothly – and not just from a technical point of view: The cooperation with the teams at MultiMaterial-Welding GmbH and KVT-Fastening GmbH was positive in every way. Otherwise the current project could not have been implemented in this way. Based on the experience so far, we are currently checking what other projects are suitable for this or which FIP parts can be developed or improved from this.”